Legacy components
50 years of microblasting innovation
Ever since the first award-winning MicroBlaster hit the market in 1968, Comco has continued to innovate and refine each and every component. Our commitment to design excellence and customer satisfaction is evident in the advancements made to each new generation of MicroBlaster.
Power. Precision. Repeatability.
The MicroBlaster has continuously evolved to meet the micro-precision blasting demands of our customers. Our blasters are tough enough to perform in high-volume production environments but versatile and affordable enough for smaller shops or blasting hobbyists.
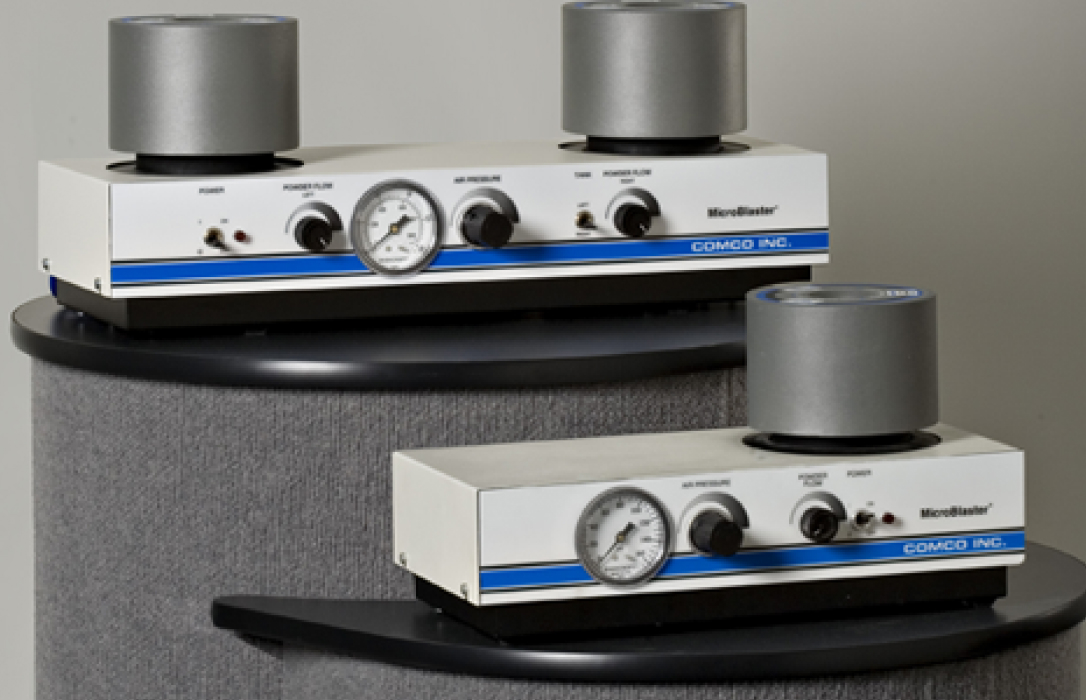
Specifications
Models:
Shipping Wt:
Height:
Width:
Depth:
Air Pressure:
Nozzle Sizes:
Requirements
Model:
Inlet Air pressure:
Air Volume:
Air Quality Supply:
Power Requirements:
BLAST WITH INCREASED SURFACE COVERAGE
PowerFlo & DirectFlo are still the same reliable micro-abrasive blasters that keep performing year after year in high-volume production environments, delivering consistent precision and results across applications.
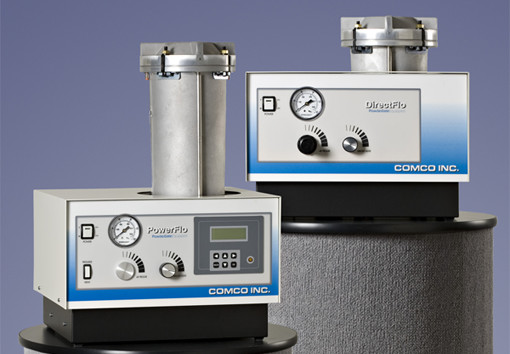
Specifications
Model:
Weight (empty) :
Height:
Width:
Weight:
Powder Capacity :
Nozzle Sizes:
Requirements
Models:
Inlet Air Pressure:
Operating Pressure:
Air Supply:
Air Volume:
Power Requirements::
BLAST IN COMFORT
Our workstations are ergonomically designed to reduce operator fatigue, featuring a spacious, well-lit work chamber and clean, quiet performance.
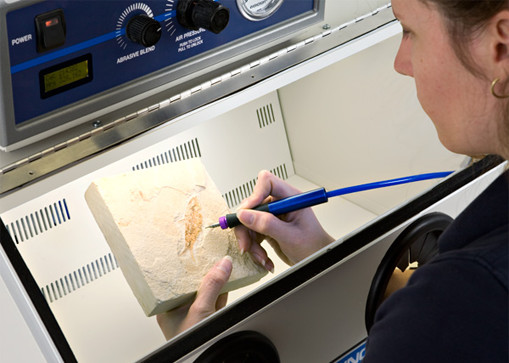
Specifications
Models:
Weight:
Dimensions:
Interior Space:
Window:
Lighting:
Power Requirements:
KEEP YOUR WORK AREA CLEAN
A clean environment with a clear visual field is essential for accurately blasting small parts. Our industrial-grade dust collection system effectively removes fine micro-abrasives and keeps air flowing through the blast chamber.

Specifications
Model:
Motor:
Air Flow :
Noise Level:
Filter Area :
Hose Size:
Dimensions (H x W x D):
Shipping Weight :
REMOVE MOISTURE AND AVOID CONTAMINATION
Keep your blaster running smoothly with clean, dry air. The micro-abrasive blasting process uses compressed air to keep extremely fine abrasive media flowing consistently.
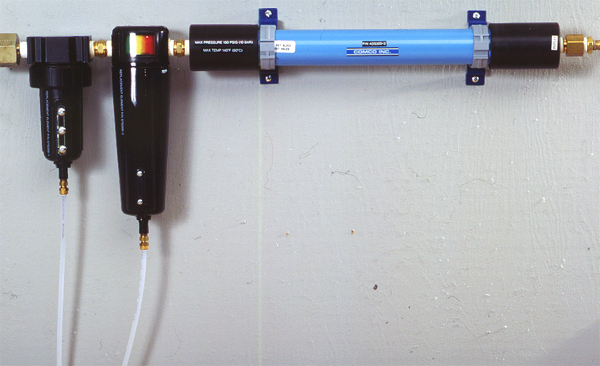
Specifications
Models:
Maximum Input Pressure:
Maximum Volume:
Maximum Moisture Output:
Maximum Air Dried Per Charge :
Requirements
Space Requirements:
Try our process
See what precision MicroBlasting can do for you. Send us a part and we’ll MicroBlast it, analyze it, and return it to you with a detailed report.
Schedule a Demo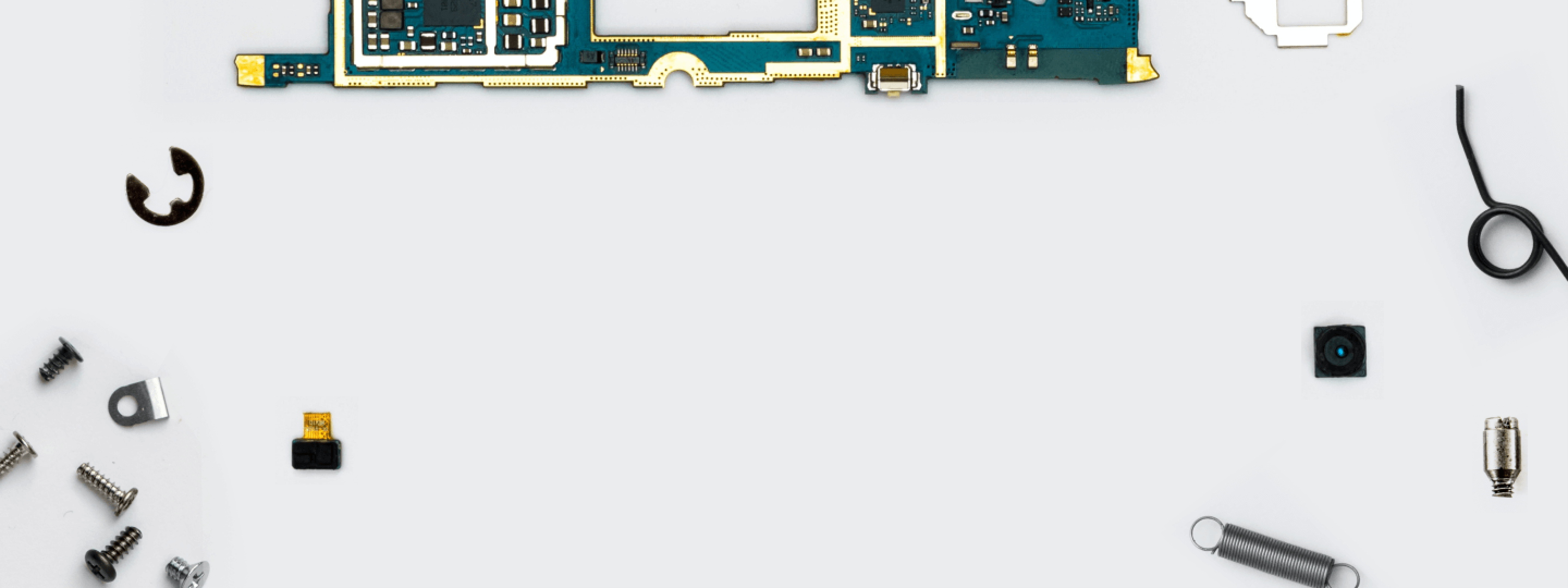